How “green” is your workplace?
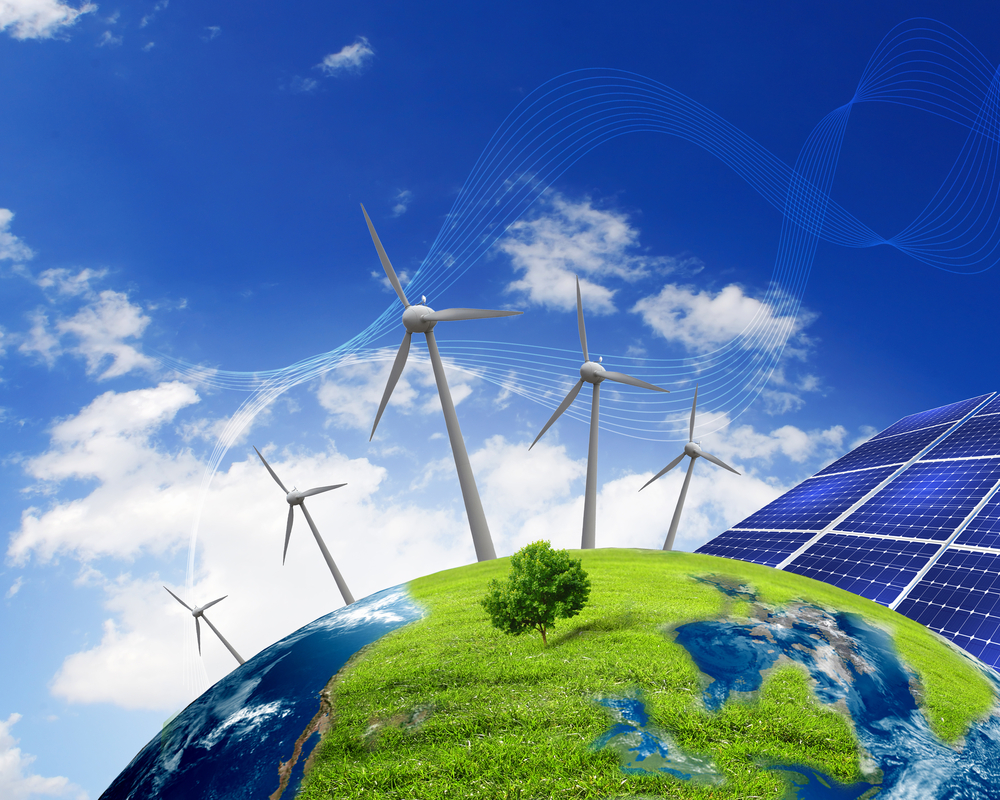
In today’s news, we see a lot about how ‘green’ a particular facility or overall business should be.
Whether it’s Tesla selling carbon credits or IKEA putting solar panels on their roof, you see it everywhere. It’s not just for some good press either, it actually does make a difference in lowering energy usage and can contribute to a better working environment.
First - electrical consumption has been a big focus.
Most people companies, Pickett/Blackburn included, have switched to all LED lighting - it’s much easier on the eyes, is a better quality light, and it simply makes it easier to see what you’re working on (very important considering the frequent quality checking required in our processes). It’s a small step in reducing the overall electricity consumption. Replacing a 60 watt incandescent lightbulb with a 6 watt LED bulb that puts out just as much light, is a 10 fold decrease in power. For our 75 fixtures, running high light quality incandescent bulbs would cost just over $1000/year in electricity cost. Switching to LED drops the electricity cost to only $108/year - never-mind the extremely long life of the bulbs, meaning less time and money switching and replacing them.
We have installed variable frequency drives on multiple AC motor driven machines, upgrading them from older on/off controls. The result is a more efficient variable speed drive and machine operation. The startup of the motor in the first place is very smooth, without the spike in electrical current, and significantly reduced noise.
Our forklift is all electric and doesn’t rely on propane. The result is cleaner air inside our shops and significantly less maintenance on the forklift system overall.
Second - recycling our materials.
Since we are machining our brass instrument mouthpieces from a single solid brass rod, this means we are removing a great deal of what comes in the door. In the case of tuba mouthpieces, it can be upwards of 92% of the material being removed. Since our machines only machine brass, we are able to keep all of the resulting chips extremely clean and uncontaminated with iron, steel, aluminum or other stray materials. The resulting uncontaminated chips are then sent directly back to the mills that produced the brass in the first place. Copper and brass alloys are extremely recyclable, and with our clean scrap we have a tight material supply loop and relationship.
Lastly - packaging.
Packaging overall contributes to so much waste in our country. Everyone gets multiple boxes from Amazon, Target, or other retailers - and the worse case: filled with styrofoam packing peanuts. We have removed styrofoam peanuts completely and have been using only recycled craft paper for bulk padding. There are still some plastic bubble sheets in our process, and we are working on eliminating those as well.
Something that is significantly under-valued at most places is the cost of your time. When you implement long life light bulbs, choose customer packaging that does not require significant time to stock and clean up constantly, and choose extremely low maintenance systems, your time goes a LOT further towards more productive and enjoyable activities instead of constantly trying to keep the company moving forward.
We still have a ways to go in reducing our energy consumption, but with small steps, not only are the short and long term costs significantly reduced, but longer term benefits include more ideal working conditions.